Magnetising Automotive Traction Motor Magnet Rotors
By Paul Fears | 04 December 2024
Bunting has designed and built a bespoke industrial magnetiser for an automotive electric vehicle application. The latest industrial magnetiser magnetises a permanent magnet rotor assembly for a high-end automotive traction motor.

Although Bunting builds a standard range of industrial magnetisers, the increasingly complex magnet assembly configurations and end-user requirements are driving the demand for bespoke models, especially in automotive and aerospace applications.
Magnetisation in an industrial magnetiser occurs when a permanent magnet material or assembly is exposed to a high intensity magnetising field, driving the material into saturation to develop the full permanent magnetic properties. The required strength of the magnetising field is considerably higher than the intrinsic properties of the material and depends primarily on the type of material being magnetised.
In this electric vehicle development and build project, the automotive company required the magnetisation of a 500mm long magnet assembly with a 200mm outer diameter. The development programme dictated that the magnet assembly could be constructed from a range of permanent magnet materials including neodymium iron boron, AlNiCo, ferrite, and samarium cobalt. The assembly would have between 4 and 24 poles.

Once in production, the industrial magnetiser will charge up to 10,000 magnet assemblies per annum. Flexibility was a primary design consideration, with three variants of the magnet assembly. Bunting’s design team adopted a bar code system where each design was easily identified prior to magnetisation and the stand-alone control would automatically set the magnetising parameters for the specific assembly.
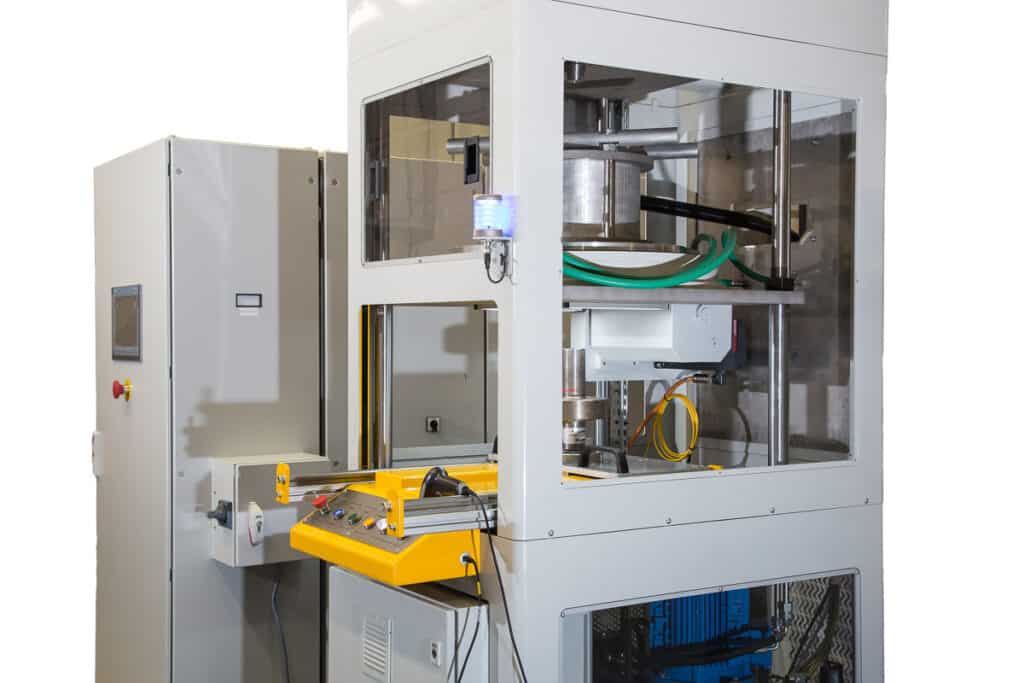
The latest industrial magnetiser consists of a magnet charger and integrated control, a chiller unit, and a magnetising fixture mounted inside a separate workstation tower. A separately mounted automatic robot handling system supports the system.
The combined magnet charger and control is 2.2 metres high, 2.3 metres wide and 1 metre deep. The separate magnetising workstation tower stands 3.2 metres high, and is 0.8 metres wide and 1.24 metres deep.
In operation, the power supply of the magnet charger delivers 6kW up to 60 kilojoules in 10 seconds on a two-minute cycle. This power creates instantaneous mechanical forces of approximately 5 tonnes, which formed a key part of the design criteria of the internal mechanics. The configuration of the magnet charger and control allows for future expansion with a project plan to operate three workstation towers, mounted side-by-side and installed in stages.
The Magnetising Cycle
In production, the magnet rotor assembly would be placed into position with a robot arm. Once the magnet rotor is engaged and held securely, it is moved up into the centre of a magnetising fixture. Then, the PLC control delivers a calculated energy level to the magnetising fixture, which generates the targeted magnetic field in the magnet rotor assembly. The magnet rotor assembly is automatically rotated and indexed along its length to generate the specific magnetic properties for this particular application.

Once the charging cycle is complete, the magnet rotor assembly moves up into the test area, where the magnetic flux is measured and recorded. On completion, the charged magnet rotor assembly moves back down through the magnetising fixture and into the original loading position for removal by the robot arm.
The growing demand in the automotive and aerospace industries for controlled magnetisation of magnet assemblies with very tight tolerances has driven the development of Bunting’s range of industrial magnetising systems. Bunting is the only company in the world to design both magnet assemblies and magnetising systems, and that unique engineering expertise enables the development of complex bespoke solutions.
“Bunting being a designer of both magnet rotor assemblies and magnetisers provides our design team with a unique perspective when working on bespoke magnetiser projects,” explained Matthew Swallow, Bunting’s Technical Product Manager. “Many of our industrial magnetiser projects are designed for a specific project and we continue to evolve the technology to meet the increasingly demanding applications in the automotive and aerospace sectors.”